The slurry thus prepared is sent
to the forming machine where the slurry is poured on the mandrels
which has number of holes and which is under vacuum and the pipes is
formed on the mandrels. The pipe thus formed is transferred to the
calendaring machine where it is pressed between the rollers under
hydraulic pressure & Vacuum System Suck the extra water of pipes
from the calendaring machine, the pipe is taken to the extraction
trolley and pipe is removed from mandrel, which again goes back on
the forming machine. |
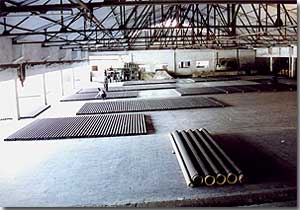 |